Vi gir deg det siste innen robotikk, kontrollteknologi og drivteknologi. Velg mellom et bredt spekter av produkter og tjenester som er både innovative og skalerbare. Vi lager komplette løsninger på dine vilkår.
Highly flexible automation for large-scale production of e-bike components
Investment in e-mobility
Morat Swoboda Motion has launched into the age of electromobility with a pioneering automation concept. The manufacturer of drive components for electromobile applications – founded in Nowa Ruda, Poland in 2018 – erected a production facility on a greenfield site.
Morat Swoboda Motion is a joint venture between the Franz Morat Group and automotive supplier Swoboda. For over 100 years, the Franz Morat Group has been among the top drive technology specialists, and manufactures everything from gear wheels to complete drive motors. With a workforce of 4,200 Swoboda develops and produces innovative high-precision components and systems for the automobile future.
With the founding of the joint venture, the two companies have set their future course in the direction of e-mobility. Both the Franz Morat Group and Swoboda have acquired experience in the manufacture of components for electric drive units. “The first joint contract for the supply of gear components for e-bike motors was not only the biggest in the history of the Franz Morat Group, it was also a major challenge for a medium-sized company. That’s why the joint venture was the best solution for all involved,” explains overall project manager Stefan Mayer.
The specific challenge consisted of constructing a manufacturing plant, planning and setting up the production lines and recruiting qualified personnel – all within a tight time frame. Mayer recalls: “There was only a six-month interval between order placement and the ground-breaking ceremony in July 2018. The machines were delivered to Nowa Ruda in November, and the first samples left the plant in March 2019.”
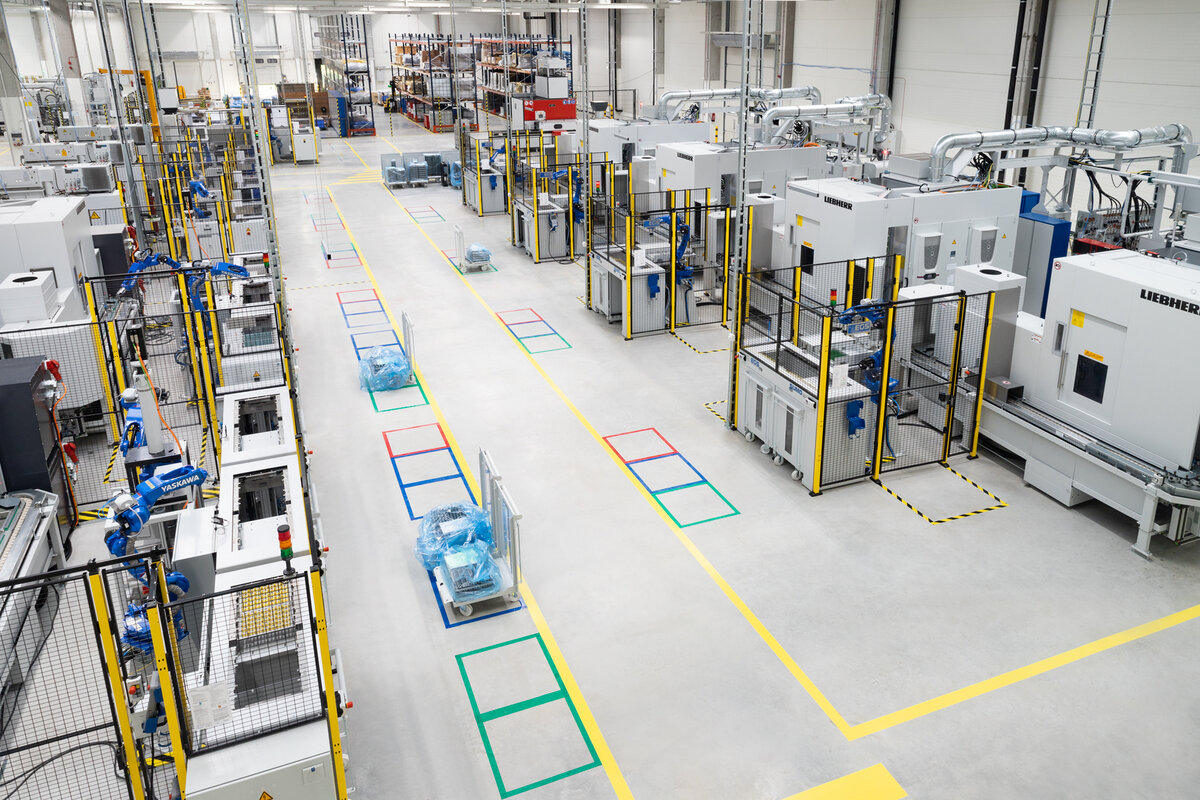
Automation solution in a class of its own
The search for a suitable automation strategy for intelligent and flexible linking of the entire machine park proved to be a major challenge. Moreover, because it called for the highest possible degree of automation with minimum manpower deployment, a suitable fully automatic loading solution had to be found for each machine.
The ideas that were initially discussed consisted of a number of detailed solutions from different manufacturers, but these failed to fully satisfy expectations. However, the presentation of a concatenation concept by Donaueschingen-based EGS Automatisierungstechnik secured the final solution. “Indeed, we were surprised to find that our complex assignment could be resolved using standard EGS modular components,” says Mayer.
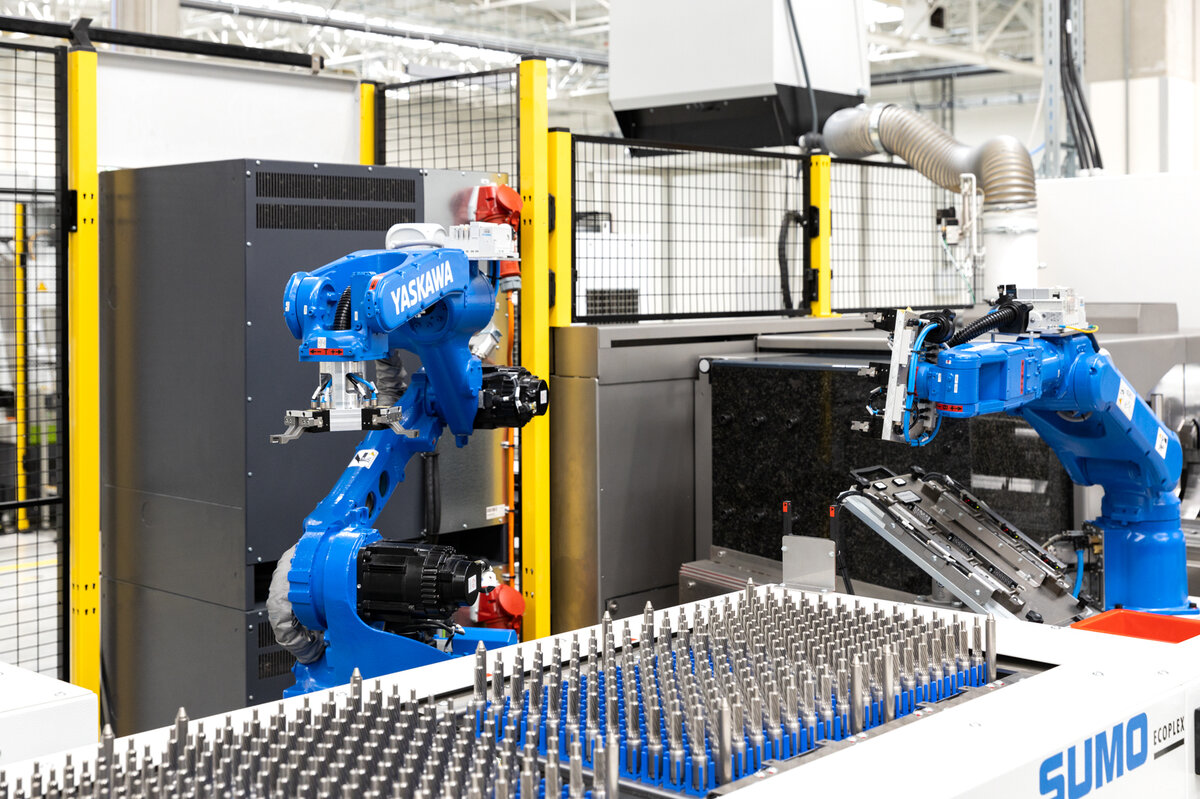
Ingenious system of machine automation and interlinking
Hartmut Pfalzgraf from the EGS sales team recognised immediately that all requirements could be optimally satisfied with the SUMO Ecoplex2 palletizing system: “Our innovative universal system has two trolleys for stocking parts and a Yaskawa MOTOMAN robot for handling parts, including machine loading and unloading. This enables us to simultaneously automate and interlink machines, and we remain highly flexible due to manual transport of the trolleys.”
The key to simple concatenation of machinery at Morat Swoboda Motion lies in the use of identical system pallets that can be adjusted to the respective part dimension by means of component-specific mountings and spacers. Once all workpiece carriers of a trolley are filled with machined parts, a worker removes the trolley, pushes it to the next machining station and docks it for further processing. The finished parts from the previous station are the raw parts of the following one.
“This superior system is simple yet ingenious. Our wheels and shafts pass through complete production process without resorting or manual intervention. Manual transport with trolleys is the most hassle-free and secure way of transferring parts from A to B, and it is unparalleled when it comes to flexibility,” says Mayer.
This highly flexible manufacturing concept offers a further decisive advantage. Should one of the machines or robots break down, the line does not come to a complete standstill, as with a solid interlinking of production elements. Production can continue with reduced output.
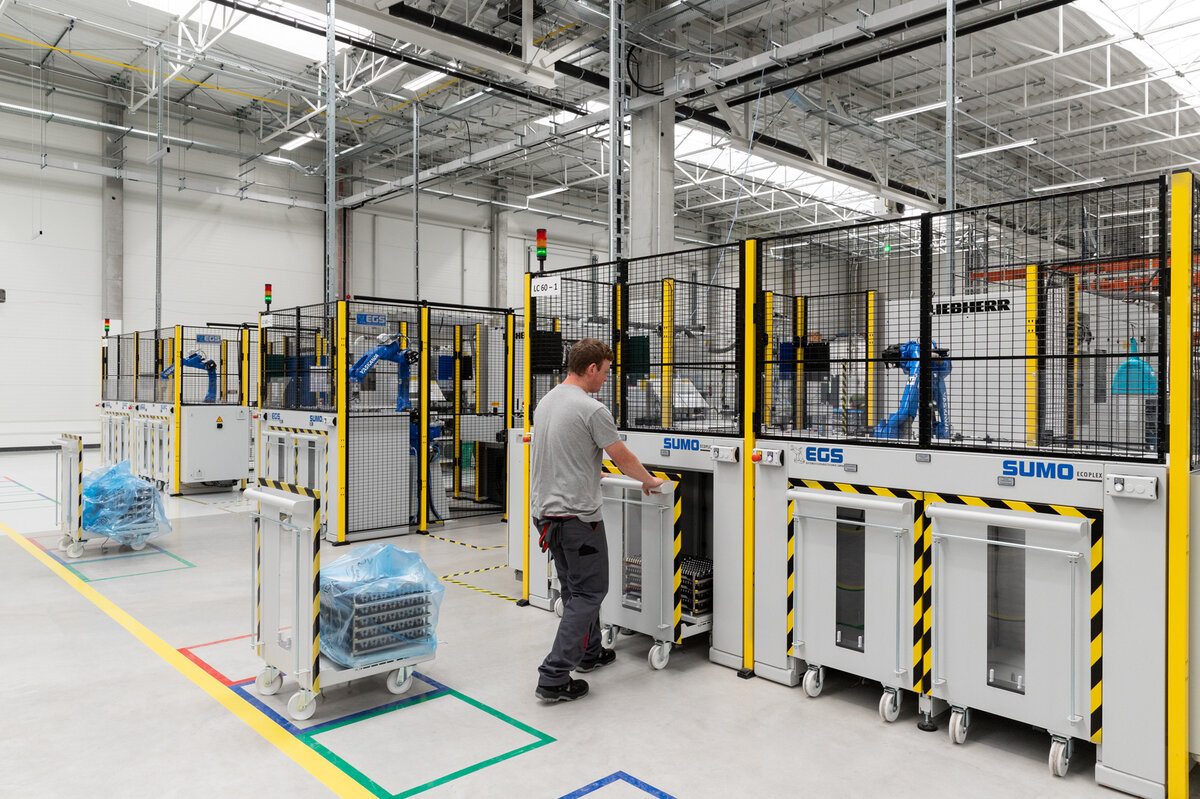
Yaskawa robots take over machine automation
Each machining centre has at least one Ecoplex2 system and at least one Yaskawa robot. Here EGS uses one robot type throughout: the proven Yaskawa MH12. This six-axis robot is the ideal candidate for machine loading: it is fast, precise, incredibly reliable and has a wide reach. Pfalzgraf comments: “The 1,440-millimetre range of the MH12 enables us to position the robot at the appropriate distance from the machine tool, with the crucial advantage that we have free access to the machine. The operator can perform service measures or, if need be, manual loading without hindrance.”
Only in a single case did EGS have to deviate in its choice of robot type. Complicated loading and unloading of a machine under strict cycle time criteria calls for two six-axis robots. The complex task is shared by an MH12 and a small, compact MH5 LSII.
“We are already using Yaskawa robots at Framo Morat, and our experience with these machines has always been the best. Because only the most reliable robots were good enough for the Nowa Ruda plant, we decided would be on the safe side with Yaskawa,” says Mayer.
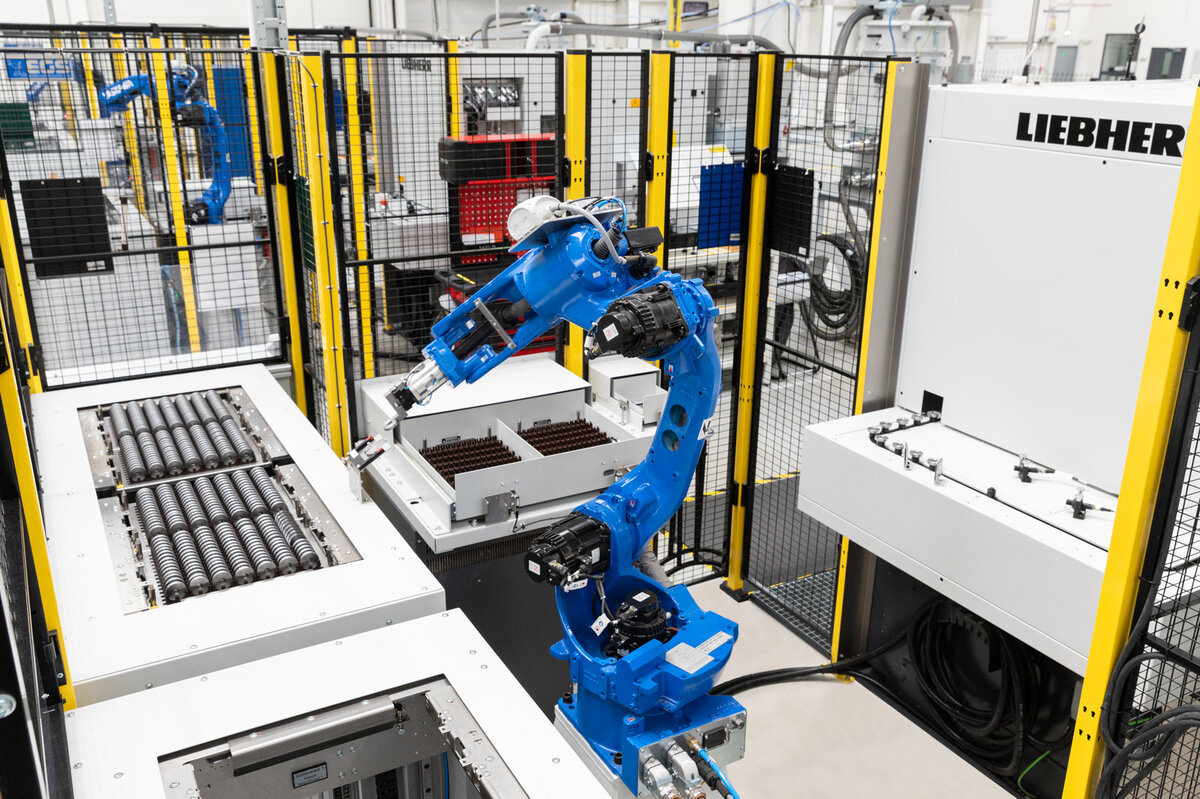
Lean production in the truest sense of the word
The high degree of automation and operator-friendly configuration of the overall system has certainly paid off in the production line with 16 Yaskawa robots and 20 SUMO Ecoplex 2 systems. The machining centre and robot communicate via the Yaskawa DX200 controller.
Quality is a central theme in Nowa Ruda. Although the machine park and robot in combination with an extremely high degree of automation are the epitome of reproducible quality, regular SPC tests are carried out.
Project manager Mayer looks at the future at Nowa Ruda with a mixture of pride and relief: “Production start-up was very successful. All components have fulfilled our expectations. And should there be a sharp increase, as forecast, in the demand for components for e-bikes, we can simply extend our highly flexible modular production,” says Mayer.
Text: Ralf Högel, freelance journalist for Yaskawa Europe; Pictures: Yaskawa
Contact readers’ enquiries Yaskawa:
Tel. +49-8166-90-0
Fax +49-8166-90-103
Contact readers’ enquiries EGS:
EGS Automatisierungstechnik GmbH
Heiko Röhrig, Leiter Vertrieb u. Marketing
Fon +49 771 898 606 27
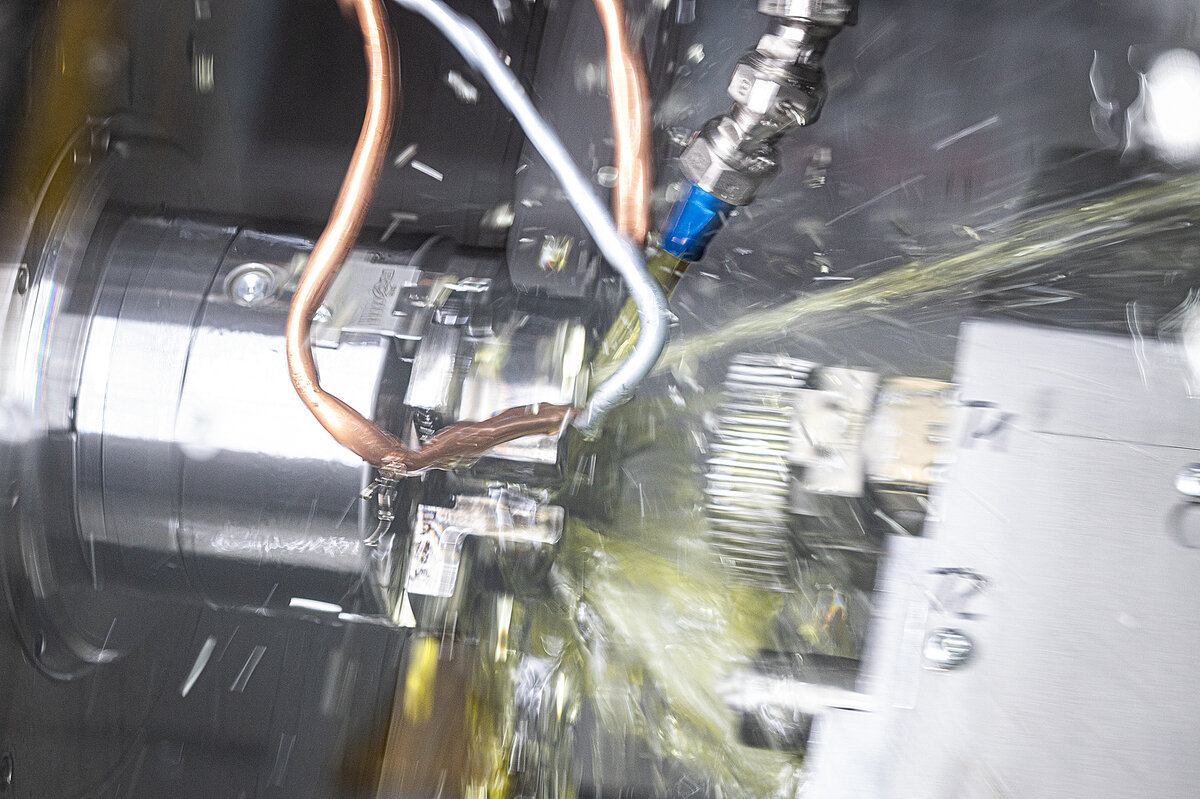