Accessories make all the differences
Robustness and synergies for heavy carpentry welding
When recounting an application, attention rarely falls on the importance of integration between the various technological components and accessories in order to ensure efficient and reliable operation. Yet it is often the synergy of all parts of the plant, together with the professional skills involved, that makes the difference. As, for example, in the 'welding system built by Yaskawa for MTS (Meccanica Tonel Sergio Srl) with voestalpine Böhler Welding unit.
A reference in carpentry and precision machining for more than 40 years
MTS (Meccanica Tonel Sergio Srl) specializes in making medium to heavy carpentry subassemblies and high-precision machining of mechanical parts on behalf of third parties, with more than 40 years of experience and a comprehensive service portfolio from design to delivery of the finished product.
In fact, its history began in 1973, when OMT (Officine Meccaniche Tonel) was founded by Mr. Tonel Sergio, on a 500 square meter area equipped with traditional machine tools such as lathes and milling machines.
The intention to enhance the production of high-precision mechanical parts led to the founding of MTS s.r.l. in 1985, which benefited from new facilities and an expansion of the machine park, enriched with state-of-the-art technological solutions.
Currently, the company has reached its second generation and employs about 85 employees in 2 production facilities. From there, it serves about 600 customers spread all over the world and operating in the fields of off-highway vehicles (earthmoving, agricultural machinery, road construction, material handling), truck and port cranes, industrial automation, industrial spare parts, and energy.
- Applications
- Arc Welding
- Products
- AR-serie
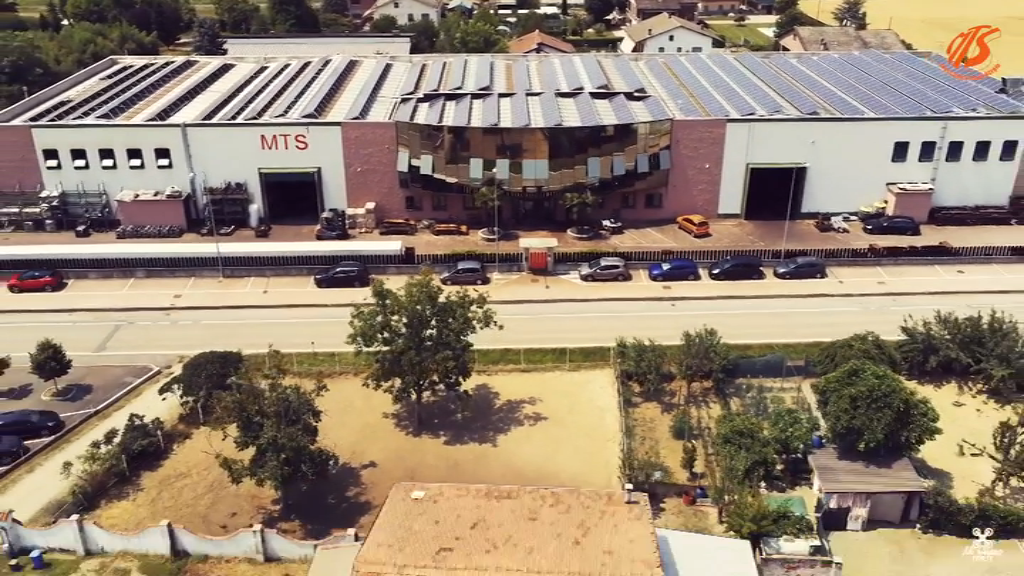
Welding, a highly robotized department at MTS
The welding department contains traditional MIG-MAG continuous wire MIG stations up to 500A, as well as highly productive robotic stations that take advantage of anthropomorphic robots enslaved by rotary tables and robots on rails that enable a wide dimensional range to be covered. All of this is operated by qualified operators who are EN ISO 1090-1 and UNI EN ISO 3834-2:2006 certified.
The collaboration with Yaskawa in the field of welding equipment began in 2010 with the aim of supporting MTS's growth also from the point of view of process automation. The first solution installed, consisting of a robotic system equipped with a 2-position Portal each equipped with two positioners and a 6-meter lathe, has recently been joined by an additional system, similar in concept but with increased operating characteristics and the addition of a random orbital positioner.
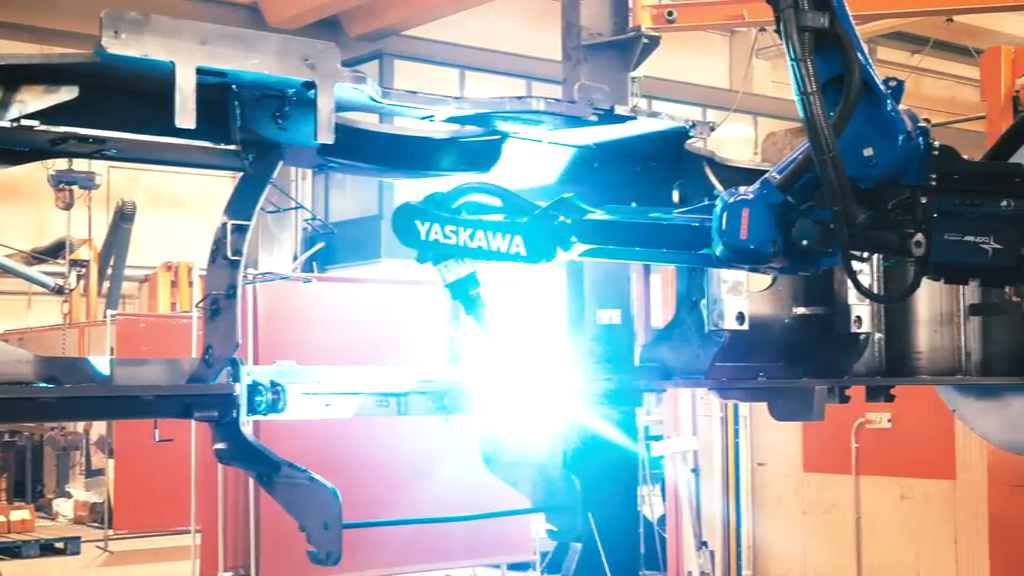
Full Welding Solution
To develop the solution best suited to the specifications of this type of processing, harmonization among all system components was critical. That is why MTS turned to a welding specialist such as voestalpine Böhler Welding.
voestalpine Böhler Welding takes a unique approach, that of the Full Welding Solution, which takes the form of offering many years of highly specialized expertise, a comprehensive product portfolio, and plant solutions whose components talk perfectly with each other.
"The result is an optimal welding process with a perfectly controlled arc designed specifically for the filler material in use, for example in the case of this application Böhler X 70-IG, a high-strength low alloy wire," explains Cristiano Bergamin, Global Sales Development Manager at voestalpine Böhler Welding. "This is a special technology we developed, which we christened Böhler Arc, that achieves the perfect match between welding process, plant and filler material."
Robust, custom-equipped cell
Moving the welding operations is a Yaskawa AR2010 robot, featuring one of the largest working ranges among those in the AR series, Motoman's family of robots dedicated to arc welding. The robot was mounted on a TSG-XYZ 8MT gantry, servo powered and fully synchronized with the robot controller, which allows the robot to move along all 3 Cartesian axes, further expanding its range of motion very significantly. This is a peripheral specifically designed for welding very large components such as those typical of excavators, containers and earthmoving machines - parts of regular MTS production.
It is precisely the robustness of the Yaskawa portals, combined with the typical reliability of Japanese robots, that was a valuable element for this application: the carpentry parts that are handled by these systems in MTS in fact require significant welds in terms of extension and thickness. All on parts that are generally already significant in size and weight.
"This system allows us to automatically weld from 60 percent up to 80 percent of the product, thanks to the programming performed off-line starting from the 3D of the element and special equipment that we have made in collaboration with Yaskawa," explains Tonel Andrea, CTO of MTS."
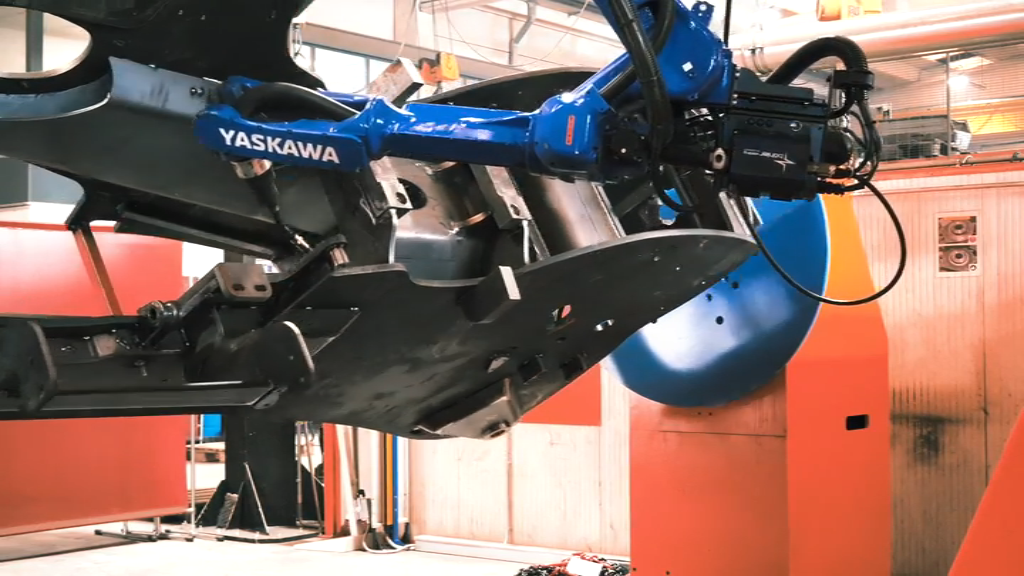
Expertise and synergy for tight timelines
"The investment was decided in order to cope with the increased production required by some important clients despite the shortage of manpower due to the pandemic," comments Tonel Daniele, CEO of MTS, highlighting in fact the importance of the timelines for the realization and commissioning of this plant.
From this point of view, the excellent synergy of the technicians, combined with the great expertise and experience of all three companies, ensured rapid engineering and commissioning of the plant. "As is normal in the concrete reality of industrial plants, a few unforeseen issues arose during the job order, but they were soon resolved without affecting the budgeted schedule," Bergamin comments.
The fact of being able to count on personnel already trained in the functions and technologies adopted allowed the plant to be operational from the very first moment of installation, immediately guaranteeing MTS important advantages in terms of optimization of welding times, flexibility of multi-shift work and increased production capacity.