Drive Technology for Flexible Packaging Machines
Packaging processes are extremely complex: The machines have to be loaded automatically, both with the packaging material and with the respective products. The automation systems have to perform a number of tasks before the finished package can leave the machine. The processes involved in the handling and the actual packing process call for a large number of powerful servo axes, which often also have to work smoothly with pick-and-place robotics. It is therefore extremely practical if the different components can be controlled using a single controller. This means that the programmer can concentrate fully on the application without having to worry about the underlying technology of the different systems.
ESATEC, a French company that specializes in packaging machines, has developed a highly flexible packaging machine in the form of the Turbomailing . This machine is capable of positioning and gluing almost all types of rigid and supple products, whether pre-cut or off the roll, onto any carrier or cardboard sheet and then folding the containers. These include, for example, perfume or cosmetics samples, gift cards, Blu-rays and DVDs as well as sachets for powder, liquids or food. A2C, the parent company of ESATEC, already uses this type of Turbomailing packaging machine in its plant in Puymoyen near Angoulême, France. The company specializes in packaging operations for the cosmetics and food industries and, owing to its machinery, is able to respond extremely quickly to a wide variety of customer requirements.
Individually Packaged Perfume and Cosmetics Samples
In Puymoyen, the new ESATEC machine is used to package cosmetics and perfume samples individually for use in promotions. Different operating modes make it possible to accommodate up to three different samples on one carrier and, if necessary, combine them with instruction leaflets as well. The samples and carriers are first fed into the machine on a conveyor belt and are brought into position in the loading station by a friction feeder. A four-axis delta robot and a further, patented five-axis pick-and-place unit place the samples on the carrier, which is then folded twice or three times. Depending on the product specification, between 6000 and 10,000 high-quality packaging units are created per hour in this way. The cycle times are thus extremely short, meaning highly responsive drives are essential. Components from Yaskawa were therefore selected both for the robotics and the servo axes for a number of reasons.
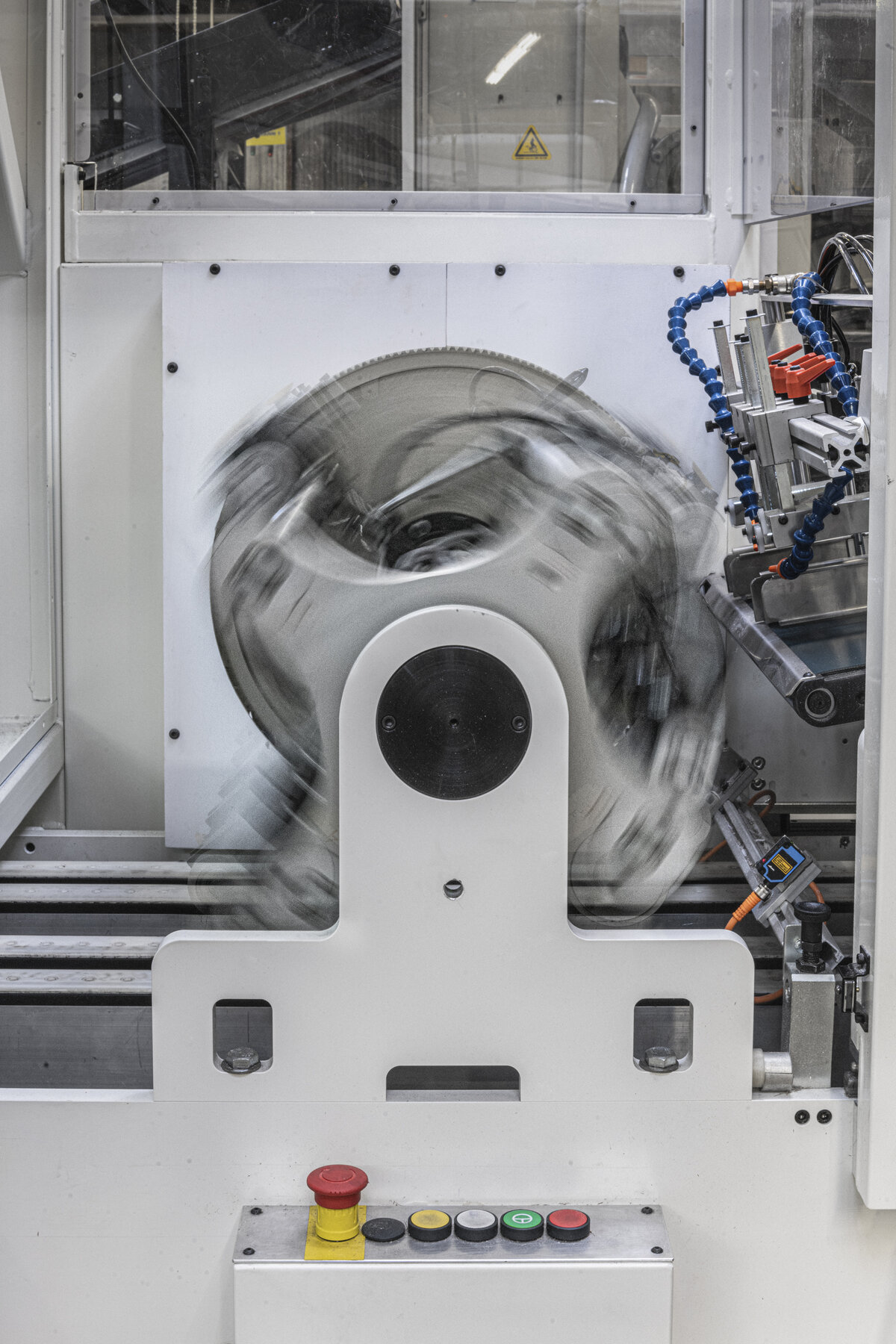
Rapid Loading Using Pick and Place
The D4 delta robot of Codian Robotics, for example, used in the packaging machine has four precisely controlled axes, making it ideal for such pick-and-place applications — it is able to position even the smallest products in a confined space quickly and with millimeter accuracy with a reproducibility of 0.1 mm. While the second pick-and-place unit is more suited to flat objects, the shape of the product is of no consequence for this robot. Equipped with a camera vision system, the delta robot picks up elements of any shape that the friction conveyor delivers.
Servo drives from the Sigma-7 series handle all other drive tasks associated with loading the machine and packaging the cosmetic and perfume samples. Two of these servo axes drive the main conveyor belt while two more ensure precisely controllable product spacing on the friction conveyor. The five axes of the patented pick-and-place unit are also moved by these drives and a Sigma-7 servo axis is installed in the folding unit.
High Power Density and Simple Start-Up
There were many reasons why these drive systems were used. For example, when developing the servo drives in the Sigma-7 series, the focus was on features such as rapid start up, high production output and maximum operational reliability, which benefited the designers of the packaging machine. There was also a large selection. The responsive AC servo motors cover outputs from 50 W to 15 kW at supply voltages of 200 and 400 V, boast extremely compact dimensions and are very quiet when running. The series includes narrow single- and double-axis amplifier modules for 200 V or 400 V in a space-saving design. These can be lined up seamlessly in the control cabinet and can easily be daisy chained if required. This reduces the installation work required. There is also a further advantage in terms of space: At ambient temperatures of -5° C to +55° C, no additional cooling is required. The servos boast an impressively high resolution (integrated 24-bit absolute encoder), high dynamics as well as functions such as vibration suppression, suppression of machine resonance frequencies and a tuningless function for simple start up.
Compact Controller for Servo Drives and Robots
The servo axes and delta robot can be controlled using a single controller. This is possible thanks to the MP3300iec RBT compact machine controller used in the Turbomailing. Yaskawa recommended it to the French packaging machine specialist, primarily on account of the standardized application programming using a single software tool with standard PLCopen and Yaskawa-specific function blocks, which are available free of charge and significantly simplify system programming. The integrated functions also include visualization tools, camera systems, conveyor tracking, and a group toolbox to support G-code, in addition to many more features. Mechanical engineers can even use this solution to implement robots without the need for a programming device (teachbox) or a proprietary robot programming language. The movement sequence of the individual axes of the robot is calculated in the controller's firmware and transferred to the robot controller. The programmer can thus concentrate on the application without having to worry about the underlying complex technology.
The servo axes can also be programmed in the same software environment. With the real-time Mechatrolink III Ethernet bus, the compact controller makes it easy to synchronize robots and servo axes. The motion controller really comes into its own when combined with the Sigma-7 servo systems: up to 62 real and 2 virtual axes can be controlled in this way. In addition to process data, the servo systems also provide the controller with status information such as a vibration analysis. This data allows conclusions to be drawn about the condition of the overall system and enables efficient maintenance planning. Altogether, this results in the best conditions for powerful motion applications such as in the packaging machine described.
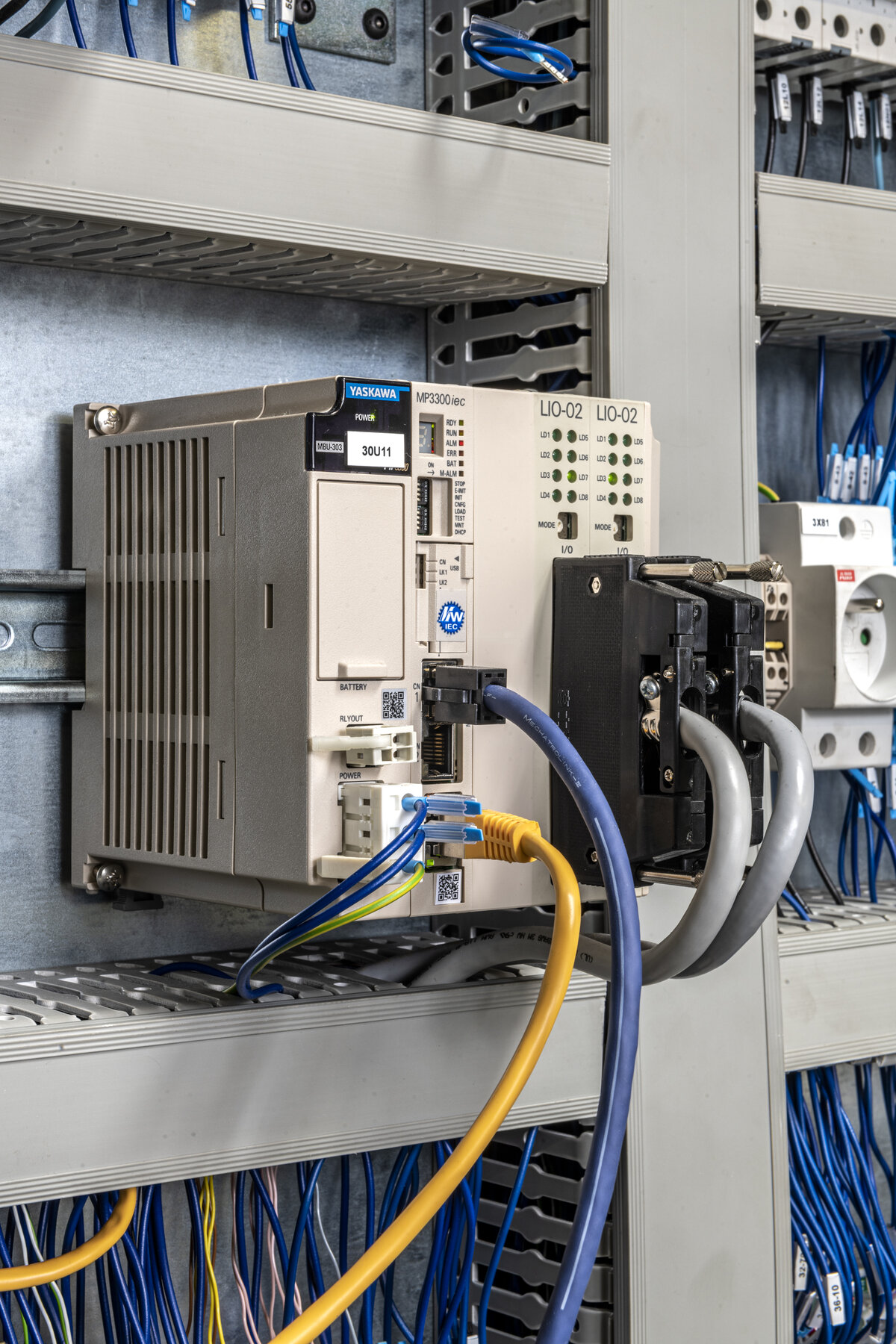